Launching a Workforce Flexibility Initiative? Here’s What You Need to Know
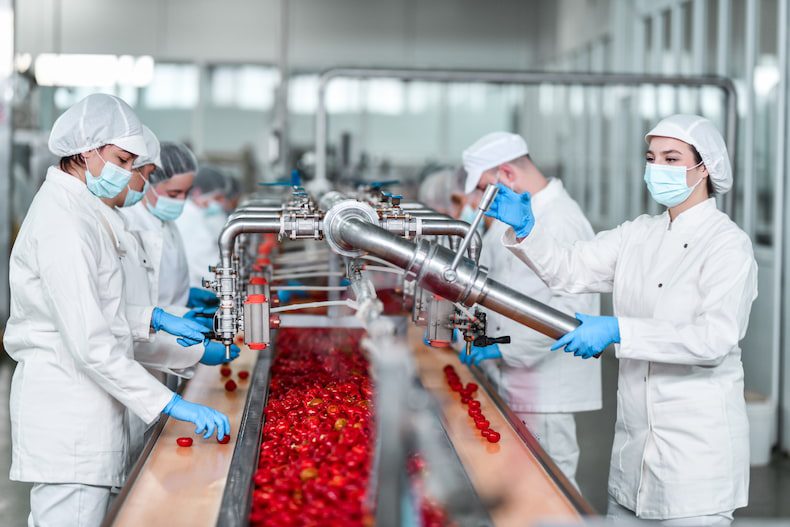
Combat Labor Shortages Through Workforce Flexibility – Part 2
We recently completed another installment of our Manufacturing Leaders Roundtable Series with four manufacturing experts from HR, supply chain, and labor consultancy disciplines, focusing on the role of workforce flexibility in helping combat the labor shortage. Part 1 of this series uncovered different definitions of flexibility, what workers value in their employers, and how training can enhance flexibility and productivity. In Part 2, our experts share valuable tips and insights on launching a flexible workforce initiative in your organization and some creative solutions that they, and their clients, have already put into practice.
Featured Panelists
- Corey Gilchrist is VP of total rewards and HRIS at Shamrock Foods. He brings 11 years of HR experience in regional and national food production and distribution.
- Kevin Schoen is a manufacturing consultant, recently retired after 34 years with General Mills. His expertise focuses on supply chain operations and helping organizations develop their people and expand workforce capability.
- Bob King leverages 27 years of experience in manufacturing and distribution in his consultancy work with mid-size manufacturers, helping them improve operational performance and efficiency.
- Doug Hammond is division president at Randstad’s Inhouse Services division focusing on high-volume custom labor solutions for a variety of large manufacturing clients.
Understand the Problem You’re Trying to Solve
Labor issues are not the same for all locations, departments, or even employees. When planning a flexibility initiative, it should be clear to you what labor issue you are trying to solve. Are you trying to increase productivity or perhaps maintain productivity but with less turnover? Improve compliance or boost attendance? Only by knowing your goals will you be able to measure your outcomes successfully.
Furthermore, you need to understand your employees’ perspectives on flexibility so you can align your objectives. “We don’t want to create a program that no one will want to use. So, consider how flexibility is defined by job function,” suggests Gilchrist. “Once you have employee input, you can create a program that better accommodates their needs while keeping business goals and objectives on target.”
Examine Resistance
Even though the pandemic may have thrown your operations into a whole new world of flexibility practices, there can still be hesitant site administrators or managers. Work to alleviate the concerns of those who are not on board in order for your new initiative to flourish.
“It can be useful to understand what sort of sacred cows might be threatened with any new labor and production change in your facility,” cautioned Hammond. “Attendance policy change was a controversial topic with our clients, especially if they were using a points system. But you can radically change a long-held system with flexible work arrangements while still holding people accountable.”
In this example, Hammond’s team developed a solution where workers were held accountable for attending the shifts they signed up for. They were allowed to work three days out of five, as long as they showed up on the days they selected. If they didn’t come in on a committed day, they were relegated to a B-tier status. A second occurrence would take them off the schedule. “You can have flexibility and accountability, but it’s a real conversation,” Hammond explained.
Start Small and Be Open to New Ideas
Our experts saw great success when their clients were open to creative ways to address
attendance or compliance issues on the floor. Those ideas can even be championed at the local level — from operations leaders to shift managers to the actual workers.
“Even though we used to put in six or nine months of self-design work with employers to deploy a new work system, today I’d think it’s better to do what I call ‘low-cost probes,’ ” Schoen advised. “Try some ideas with one shift of workers or one section of a packaging line and see what happens. I’ve been floored by workers’ willingness to try new things.”
The point our experts make: don’t waste the crisis. Start small and go from there. Create a leadership team that’s willing to take an idea and run with it, even if there might be some risks. And regardless of the project, remember to get input from and communicate with workers, while establishing guideposts to measure your gains against the problem you want to solve.
Train Beyond the Floor
To continue to expand workforce flexibility options, the role of cross-training cannot be emphasized enough. Under today’s labor shortages, it’s possible to see an entire workforce get sent home while a second line continues to run shorthanded. Cross-training labor pools builds a larger workforce that is qualified to work in multiple parts of the facility, which enables employers to optimize their labor dollar.
“We’re getting folks from a much different pool than we were hiring 15 years ago,” furthered Schoen. “But with millennials, it’s a question of what will excite them. So what skills can you provide beyond cross-training and flexibility options?”
“Our client runs a welding school within their facility,” King offered as an example. “We bring in entry-level folks, administer a testing regimen, and then move them into a paid after-work welding school that the client runs to manufacture their own welding labor base.”
Creative? You bet. So today’s organizations benefit not only from flexible skills training but also innovations that go beyond the basic floor to further boost productivity. Life skills, communication skills, and conflict resolution skills ease workforce challenges while helping workers connect with a more gratifying employment experience.
Looking Ahead
Ultimately, the pandemic forced organizations to be open to change — using business methods not thought of in the past. Going forward, the industry will see different workforces, strategies, and schedules to help reduce employee turnover. While the goals of the company will remain first and foremost, there is value in looking for creative, flexible solutions that meet both business and employee needs.
Organizations will most likely also be weighing other options ahead — to invest in automation versus expanding workforce flexibility, for example. Will they need to eliminate parts of the workforce or move portions to another part of the plant? These capital allocation decisions will become more pronounced for leadership as they balance workforce needs and productivity goals. The use of technology, whether for systems or employees, will also figure more prominently in the workforces of the future.
Conclusion
Employers that continue to conduct business as they have in the recent past will get left behind. Once you understand what employees are looking for, you can consider diverse flexibility solutions to stay competitive. While each company’s combination of strategies will be unique, the willingness to adapt, take risks, and move forward will help organizations find win-wins to the labor shortage crisis.
Shiftboard would like to thank Corey Gilchrist, Kevin Schoen, Bob King, and Doug Hammond for their valued commentary and insights in our “Combating Labor Shortages by Increasing Workforce Flexibility” webinar and supporting blog series. If you missed the previous article in this “Combating Labor Shortages by Increasing Workforce Flexibility” blog series, gain more insights in the previous post.